June 24, 2019
Engineered wood products have received a lot of attention lately. Being able to take a log, cut it, grade the individual pieces, then glue it up in a particular manner is what makes wood competitive with steel and concrete. When you consider all the other benefits wood offers, it’s no wonder there’s so much hype.
Comparing Engineered Wood Products
There are many different types of engineered wood products. When it comes to structural wood, the building blocks include dimensional lumber, strands, flakes and veneer. Each building block is processed differently and there are advantages and disadvantages to each.
If you start digging into all the products available out there, such as glulam, LVL, LSL, PSL, etc., you’ll find that the veneer-based products tend to outperform the lumber-based product in strength and stiffness. Why is this?
There are couple explanations here. One is how it is processed. Wood can be quite strong and stiff, but it is also filled with natural defects such as knots from limbs. So, with lumber you are cutting blocks out of the tree and you tend to get a larger portion of knots, and the strength is lowered.
Veneer is peeled off the log with a lathe, slicing through knots typically at an 1/8” per rotation of the log on the lathe and dispersing defects throughout a whole sheet of veneer. Dispersing the defect doesn’t allow it to have as big an impact as it otherwise would. In the picture below, you see the same knot at different locations on the sheet indicating one full rotation of the log in the lathe.
Increased Strength in Layering
Another reason veneer products can achieve higher strength values than lumber is that veneer is thin and therefore has more layers in the same cross section. This distributes the defects as well.
A glulam beam also benefits from this layering, but veneer has more cards in the deck, per say. Using this metaphor, there’s a higher probability that there will be a high card next to low card resulting in a higher average. This shows up in testing. Some beams will break at a very high load and others at a very low load. The smaller the variability the higher you can justify the strength values.
Veneer’s Efficiency Over Lumber
Some other differences you get with veneer is that there is no saw dust and you get more wood fiber recovery from the log. With lumber you are sawing the shapes out of the log and, thus, there is a saw kerf that goes to saw dust rather than lumber. Also, you are cutting square shapes out of a round tree. Peeling veneering takes advantage of a round log, allowing you to recover more of the fiber.
Peeling also allows you to use smaller trees. You can get six to eight full size sheets of veneer (4’x8’) out of a six-inch log, creating value for those smaller trees in a dense forest understory. This can have a positive environmental impact by using low impact harvest methods, such as thinning. In turn, this reduces fuel load in tree stands that are very susceptible to these large forest fires we are seeing today. Perhaps, we can start managing government land to help reduce forest fires and bring more prosperity back to our rural communities.
Less Energy Use in the Drying Process
We can also see the benefits with veneer in the drying process. Veneer, being thin, dries to a 4-6% moisture content in as little as four minutes. This means it takes very little energy to dry, where lumber will take several hours to days to get to 18% moisture content.
When it comes to engineered wood options there are certain advantages that can be gained with veneer-based products. The strength and stiffness of wood can be leveraged to a greater degree; plus, we see environmental benefits. However, there are advantages to lumber-based products, as well, and lumber has proven to be a viable choice in many circumstances. The best choice is to use wood first, and steel and concrete when required.
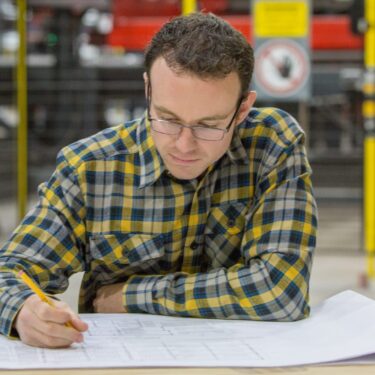
Subscribe
We’ll send you a notification when a new story has been posted. It’s the easiest way to stay in the know.