February 1,2021
Last November the company began erection of a new chipper room and storage building at our plywood plant. The primary purpose of the new building was to enclose a newly-installed chipper used to breakup trim from our panel sawline. At the same time we realized that additional storage space for parts and equipment would be helpful at the facility. We engage Crow Engineering, who we have partnered with on engineering design for a couple past projects, to help design the structure.
The building was designed with a mix of 3”, 4”, 6”, and 8” Mass Ply Panels. The wall panels were 3” and 4” thick, depending primarily on the size of the opening cut into the wall such as a large overhead door. A mezzanine floor was designed at 6” and beams and columns were standardized on 8” product.
Wall panels were designed so that the wood grain was running vertical to the wall, which allows the major force axis of the panel to provide structural support for the building. Spline joints were utilized on the wall and roof panel sections to connect panels together and create the building envelope.
Adams Construction erected the building in November. The concrete and curbs had been completed previously as weather permitted. Erection of all Mass Ply Panels took 5 days. Windows, doors, and exterior sheet metal was installed, as well as the infrastructure for the building. Carter’s Spinkler moved a sprinkler bell house as part of the project, our own electricians performed all the electrical work, and Adams finished all remaining building elements.
Lessons
As with any project lessons are learned during the construction.
- The weather was extremely wet during the construction process, and the steel connections and some of the fasteners on the project stained the Mass Ply Panels. This was an appearance issue that, while not as important on an industrial project like this, can be a serious issue in other projects and needs to be addressed.
- Typical concrete does not meet the same tolerances as our Mass Ply and where the concrete and wood panels meet must be constructed carefully. When installing one of the wall panels, it was found that a curb poured for the building was about 1/8-1/4” high. This would not allow two of the wall panels to fit snugly together, and the top wall ridge was not straight. The panel had to be cut on site to fit properly.
Thanks to everyone that worked on this project. The space is clean, quiet (even with a chipper nearby), and will provide helpful long term part storage.
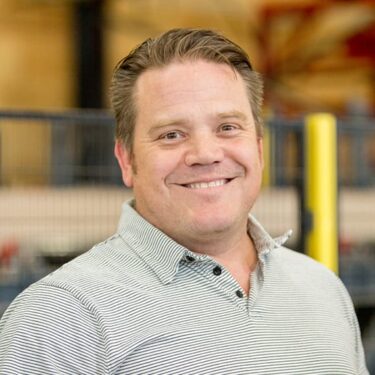
Subscribe
We’ll send you a notification when a new story has been posted. It’s the easiest way to stay in the know.