As a “part 2” discussion on robots in the wood products industry, I’d like to dive in to how robots have long been helpful in labor-intensive positions dealing with higher-value products; in our case, this applies to patching for visual grade veneer products. Robots are quite often seen in veneer manufacturing operations such as ours. This is largely because wood products are a natural raw material and are therefore variable. We aren’t dealing with widgets purchased off a shelf and packed neatly and consistently in boxes. We are working with a natural material that is much more difficult to handle. As we see technology continue to improve, the future of robots at Freres looks promising.
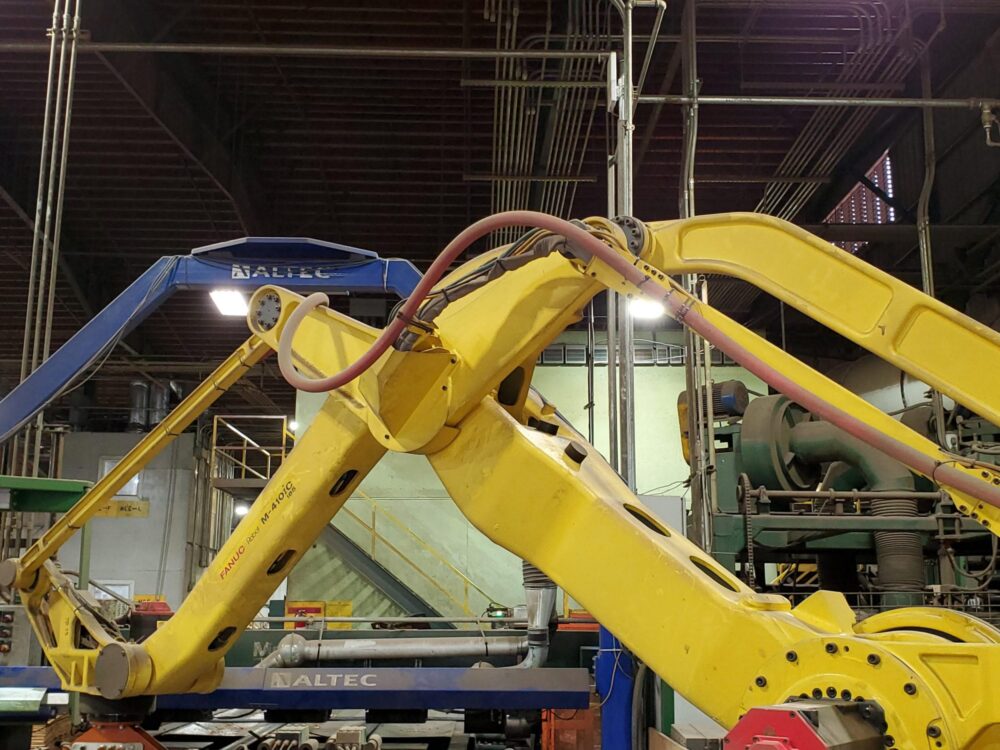
Over the last 10 years, vision technology has evolved significantly and is now starting to overcome many of the issues that were once found in robots handling products. Cutting-edge vision software can more easily identify and account for split sheets, large defects, and skew. End of Arm Tooling has also become more sophisticated, and veneer and plywood lend themselves particularly well to handling with vacuum technology.
Robots Versus People
Both machines and robots have allowed for significant increases in worker productivity. Said more simply, fewer people can produce more product with the help of machines. This doesn’t mean that our manufacturing floors are empty of people or ever will be. Our industry is extremely labor intensive, and jobs are produced along the entire supply chain. We rely on workers in forest management planning, harvest operations, transportation of logs to the mills, and manufacturing. Many people are needed for mills to produce the variety of wood products as part of their primary or residual operations.
In fact, with Oregon’s unemployment rate at a historical low of 4%, the challenge has been attracting employees to our industry. Wood product facilities are typically located in rural areas with fewer people, and therefore fewer employees to choose from. Often people will choose to work in more urban areas instead of commuting to rural areas for employment. In order to attract people to available positions wages have increased steadily over the last few years. This is great for the families supported by these jobs and their community, as long as those companies can remain competitive in a global market.
Robots in the Future
I believe in the future you will see wood products companies adopt technology in entry-level positions with a high number of employees. These positions are typically in green chain or dry chain operations and are also hard! Attracting new employees and keeping turnover low can be a struggle. These labor-intensive jobs have higher injury incidents, as employees with less experience are physically moving and stacking wood products.
These jobs will not disappear but may possibly become more attractive positions. If robots can take over the manual part of the job it may increase productivity, decrease cost, and decrease risk of injury. Then the positions become less arduous, provide more fulfillment, and provide a more attractive wage to those monitoring the sophisticated machines. The young, computer-savvy employees today are up for the challenge, and I believe it could help restore rural economies that have suffered for too long.
Subscribe
We’ll send you a notification when a new story has been posted. It’s the easiest way to stay in the know.