One of the keys to success in mass timber is the ability to cut and route panels, beams and columns, so that when they arrive on the jobsite they are ready to install without additional labor. Whether manufacturing on the product is required for mechanical, electrical, or plumbing (MEP) penetrations, to allow for connections, or simply to cut pieces to correct dimensions, the capabilities of modern CNC machines are essential to the success of mass timber projects.
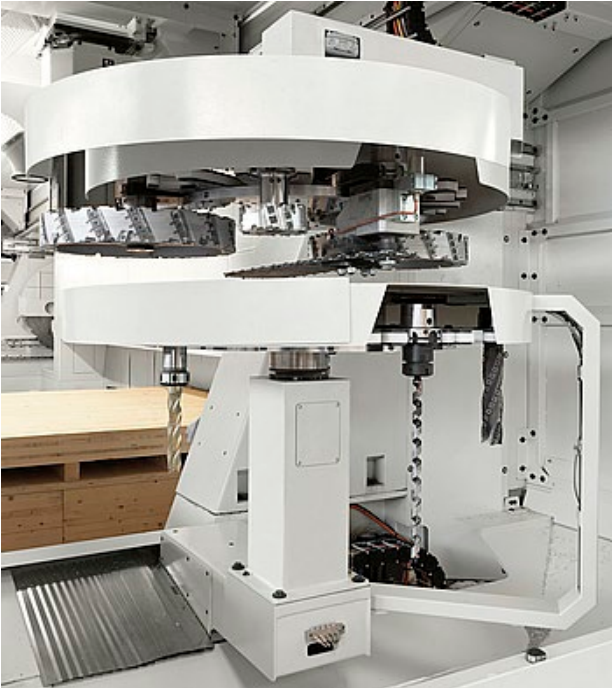
Our Mass Ply Panel facility has utilized a Weinmann WMP 240 CNC for panel processing since we began operation in 2017. After a significant amount of downtime last year due to the inability to source parts, we learned that we would have limited support for the machine in the future. This forced us to consider a replacement machine. The universe of large scale, mass timber CNC manufacturers is not large, but we were able to research a variety of options and decided on the SCM Area XL. As luck would have it, a fortuitous chain of events allowed for delivery of the equipment in December of 2023, and we are in the process of commissioning it.
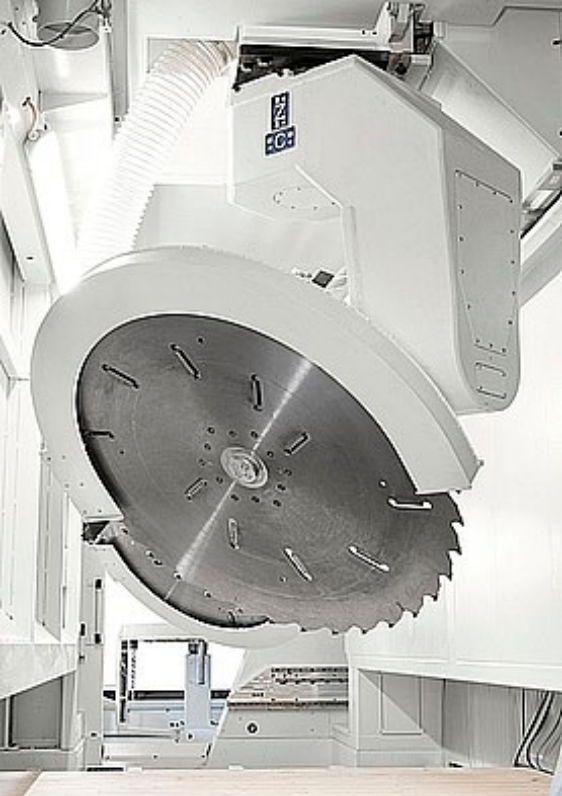
The SCM Area XL has completely different features than our Weinmann. One of the first glaring differences is that the Area XL has the option for two large cutting heads at 63 kw, where the Weinmann WMP 240 had one 30kw spindle for cutting with a 920mm saw and a 24kw main spindle. The additional horsepower on the spindles is beneficial for the machine feeds and speeds, but also allows for a wider variety of larger tooling that we were not able to use on our existing machine due to clamping pressures and horsepower of the spindles.
An example would be disc-cutting tools like the one shown below. These disc cutting tools can speed up routing operations, such as those for spline connections, by cutting a width of three inches in one pass instead of a typical router bit, which is one and a half inches and would take twice as many passes. We hope that this, coupled with the ability for each spindle to be operating at the same time, will dramatically speed up basic panel connection operations.
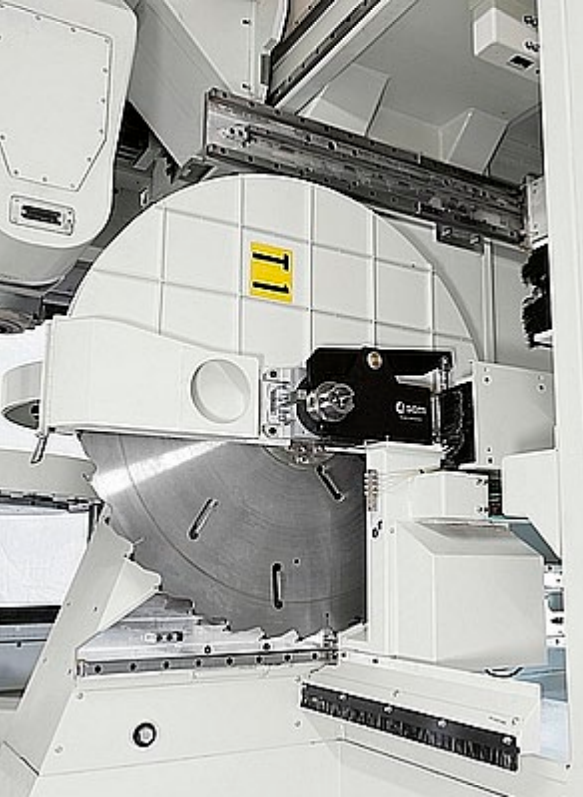
Another difference is that each of the spindles on the Area XL has a Rapid10 position and a Rapid18-position tool holder, whereas our current machine was limited to a total of 18 tools. The large saw on the SCM is 1150mm compared to the 920mm on our existing machine, which will increase the thickness of the panel we can process – up to a maximum of 14 inches. The secondary saw has also increased in diameter size to 800mm from 640mm on the Weinmann. Another great feature added will be the use of a chainsaw aggregate for corner cut outs of doors and window openings.
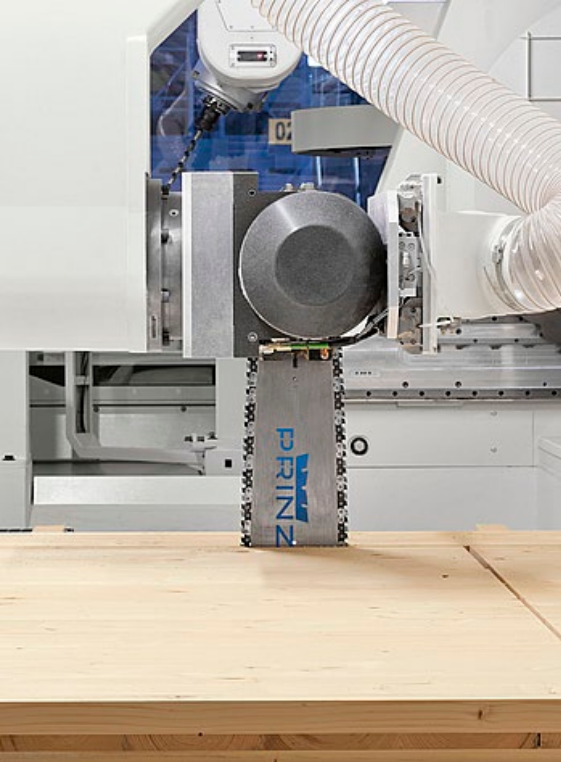
One of the changes our operators are most looking forward to is the addition of a chip removal system, which conveys chips from the CNC bed to one of the dust collection systems to allow for quicker, easier cleanup and dramatically reducing the manual labor involved.
There are many good CNC manufacturers for mass timber manufacturing. Both SCM and Hundegger, for example, have machines capable of processing beams up to 24 inches thick and 48 inches wide, which are the largest beams and columns that we can manufacture. Members of the Freres team will be traveling to Ottobeuren, Germany, in the next week to learn more about their Robot Drive beam CNC. We appreciate their hospitality.
Redler system for under table chip cleaning during the cutting process of panels.
A quick thanks to the SCM installation team who has been onsite from Italy for the last few weeks. The installation is looking good, as we are eagerly anticipating processing our first panel.
Subscribe
We’ll send you a notification when a new story has been posted. It’s the easiest way to stay in the know.