Those of you who follow our blog are most likely aware that we completed our first all-MPP mass timber warehouse and received occupancy at the beginning of October. From the beginning, this project has been a case study to demonstrate that a mass timber warehouse is not only possible, but that it can compete in cost with traditional Pre-Engineered Metal Buildings (PEMB) and Concrete Tilt projects. There are some key metrics of the project to share that we hope inform those considering their next warehouse design:
Building Type | V-B Construction | Square Footage | 57,936 | |
Grid Spacing | 40’ x 48’ | Height | 30’ to ridge, 25’ to purlin | |
Wood Package Fab | 17 days | Structural Erection | 6 weeks | |
Building Package Cost | $1,257,024 | Package Cost/sqft | $27.70 | |
All-In Cost | $6.9 million | All-In Cost/sqft | $119/sqft |
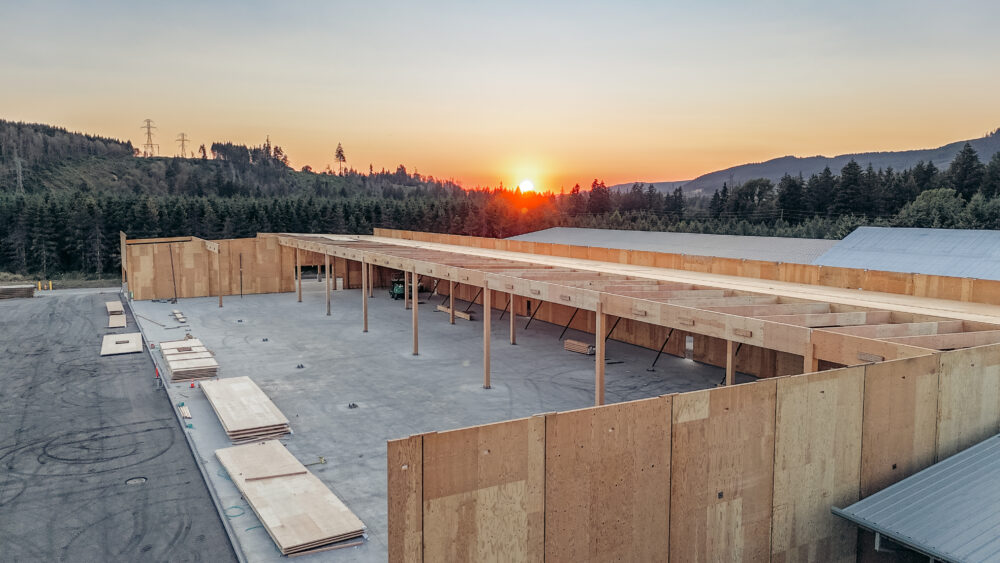
We believe that this project met its goal of demonstrating that Mass Ply cross laminated timber (CLT) products are cost-competitive with both PEMB and concrete tilt construction. Beyond the hard costs listed above, It’s also important to consider the environmental benefits of constructing with mass timber. Some environmental metrics to consider related to this project:
Volume of Wood | 1,047 m3(36,958 ft3) | North American Forest Grow this volume of wood | 3 Minutes | |
Carbon Stored | 1,110 metric tons | Avoided CO2 | 429 metric tons | |
Total Carbon Benefit | 1,539 metric tons CO2 | Equivalent to | 325 cars off the road for 1 year |
Even when considering the hard costs and environmental benefits, building with wood offers additional advantages that make it a compelling choice.
Speed of Construction- Our general contractor on this job, CD Redding, has indicated that our erection schedule of 6 weeks was approximately 3 months shorter than that of a concrete tilt project, because all of the wall panels were constructed prior to the slab being poured. This is not possible with concrete tilt, which requires the slab to be complete so that the walls can be poured on the slab.
Aesthetics- Yes, we are biased, but we don’t believe that a PEMB or a concrete tilt building provides an environment that is as comfortable or enjoyable to work in as wood. The wood on the interior is open for all to see and is unmarred by z-girts running at regular intervals which also leave ledges for dust and debris. Our employees have commented that the building feels warm even though it is an unheated space.
Sustainability- The average block diameter used to produce the engineered wood products for this warehouse are about 9-10 inches. The small diameter timber used in our structural mass timber and cross-laminated timber is exactly the material that needs to be removed from our over-stocked forests, helping to fund other forest management projects aimed to reduce the chance of the next catastrophic wildfire.
If you are considering a new industrial space, data center, or warehouse, please reach out to our sales team (sales@frereswood.com) to discuss the benefits of building with wood, and specifically our mass ply panels and lams. We provide regular tours of both our facilities, and we would gladly give you a tour of this new warehouse so that you can see the future of sustainable construction for yourself.
Subscribe
We’ll send you a notification when a new story has been posted. It’s the easiest way to stay in the know.